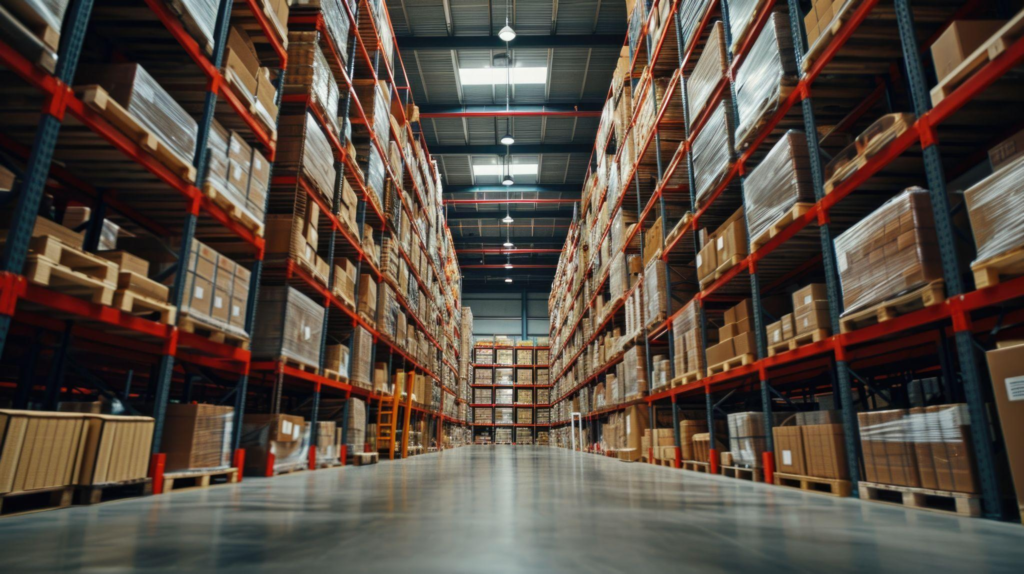
Warehouses and storage spaces are paramount to businesses producing physical goods, keeping products fresh and intact until they’re ready for transport. Properly storing and organizing inventory is also critical for efficiency, safety, and meeting customer demand.
But as your business grows, you may find yourself needing more space in your current facility. You must carefully evaluate your space requirements and options to set your business up for continued success.
The good news is that you probably won’t run out of choices. According to recent figures from Statista, there were over 20,000 warehousing and storage providers in the US as of 2021. This figure is increasing annually.
When the time comes to expand, finding the right space suitable to your requirements can be challenging. Here’s a guide to help you get started.
Table of Contents
1. Analyzing Your Inventory And Space Needs
The first step is taking a close look at what you currently have in stock across all product lines and analyzing sales data and forecasts to project future inventory needs. Get input from department heads on expected inventory growth in their areas. You’ll want hard numbers on:
- Current inventory classified by product type, units, dimensions, and turnover rate
- Growth trends and sales forecasts by product
- Seasonal or promotional stock requirements
- Optimal stock levels and restock cycles
Map out your current facility space and how it’s being utilized. Determine what’s working and what isn’t. Then factor in additional space needed to accommodate the anticipated expansion. Carefully measuring and planning now will help prevent constantly having to move or acquire more space again soon.
2. Assessing Your Facility Options
Once your space needs are clearly defined, the real property hunting begins. You have three options: leasing a new space, renovating your current location, or purchasing a building.
- Leasing Warehouse Space
Leasing provides more flexibility to change locations once your business outgrows the space or your needs shift. Typical warehouse leases run for three to five years. Negotiate optimal terms for renewals and expansions now so you’re not scrambling later.
There may be more competition for quality warehouse properties in fast-growing industries or locations, so start exploring options well before needing more capacity. Check out Storology Storage Roswell NM, if you’re operating in New Mexico and similar companies in your area.
Also, budget for expenses beyond rent, like shelving installations, any needed temperature controls or specialized power sources, and compliance measures.
- Renovating And Expanding Your Current Site
Sometimes, the most practical solution is acquiring adjacent space or renovating parts of your existing building to incorporate additional square footage. This allows you to keep current operations running smoothly at that location while expanding is completed. It also provides continuity for your workforce. Ensure the location can accommodate physical additions if going this route.
- Purchasing A New Building
Buying your own warehouse or distribution facility can make more sense for stable growth and long-range planning, provided you secure proper financing. This route allows you to customize the space to your current and future requirements.
By designing everything around your business model rather than needing to retrofit later, you can maximize productivity and efficiency more upfront. Make accurate growth projections so you don’t have to relocate again soon after purchasing.
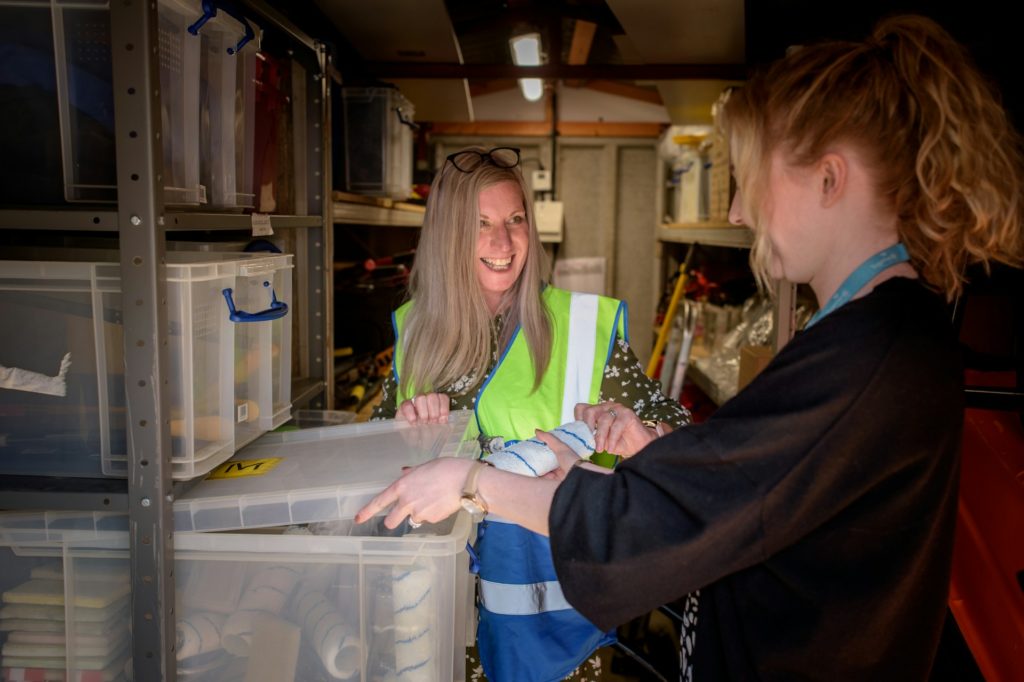
3.Considering Your Current Operations And Future Requirements
How you operate plays a key role in space planning. Here are some important considerations:
- Workflow And Layout Needs
Your facility layout and inventory management processes should dictate your space requirements. Chart out required work zones, inventory slots, aisles, and dock space. Any bottlenecks or inefficiencies in your current layout should also be addressed in the new space.
- Technology And Automation Goals
Today’s technologies can maximize productivity and storage density, from barcode scanners to warehouse management systems to autonomous mobile robots. If you foresee significant automation in your future operations, ensure any new facility accommodates the necessary charging stations, interfaces, clearances between racks, etc.
- Smart Procurement And Inventory
Your purchasing and replenishment strategies should directly complement your inventory expansion plans. Carefully analyze how your planned procurement strategies translate to actual square footage requirements. Work with procurement teams and suppliers to align inventory ordering and delivery schedules to maximize warehouse space. The right procurement philosophies that match your inventory growth goals can optimize turnover and return on facility investments.
- Compliance Regulations
Depending on your location, inventory items, and business sector, you likely must comply with regulations, including zoning, fire and building codes, and environmental standards, to name a few. Any potential spaces will have to meet those requirements from the outset.
4. Selecting The Best Option For Ongoing Success
Choosing warehouse space comes down to balancing your budget with meeting current and future inventory storage and handling needs in the best way possible. Thoroughly examine each option’s costs, risks, and benefits, along with how well it supports your current and future operations. The right solution will provide the room for your inventory and operations.
Why You Might Need To Expand Your Inventory Space
There are several compelling reasons growing businesses need to ensure they have enough warehouse capacity to handle increasing inventory demands:
- Meet Rising Sales Demands
As sales continue ramping up, you need sufficient inventory to fulfill orders and avoid stockouts that result in lost sales. Customers will go elsewhere if products are frequently out of stock. Expanding inventory alongside growth is critical, but that stock has to go somewhere.
- Buffer Against Stock Shortages
No one wants to scramble when a key item is back-ordered. Maintaining higher safety stock levels helps shield against unpredictable supply chain disruptions. But buffer inventory still takes up precious floor space.
- Flexibility For Seasonal Spikes
Retailers and other industries see large seasonal spikes where inventory levels can double or more. Having the facility capacity to house excess off-season items and the influx of seasonal stock allows businesses to capitalize on sales opportunities instead of losing sales.
- Space Optimization And Efficiency
Lacking adequate square footage doesn’t just limit inventory capacity; it hinders overall warehouse operations. Cramped quarters reduce picking speed, order accuracy rates, and workforce productivity while increasing extra shifts or temporary overflow facilities costs. The right expanded space tailored to your processes enhances efficiency.
The Bottom Line
Managing expanding inventory is a good challenge, as it indicates a thriving business. However, considering the variety of options available, it can be an equally frustrating exercise. Considering the importance of storage spaces in running a successful business, it’s vital that you know how to pick the right one.
Assess where your business is now and where you want to take it in the coming years. Compare different facility options against your operational requirements to find the ideal home for your growing stock levels. With adequate space and smart storage solutions, you’ll be equipped to efficiently meet the rising customer demand without breaking the bank.