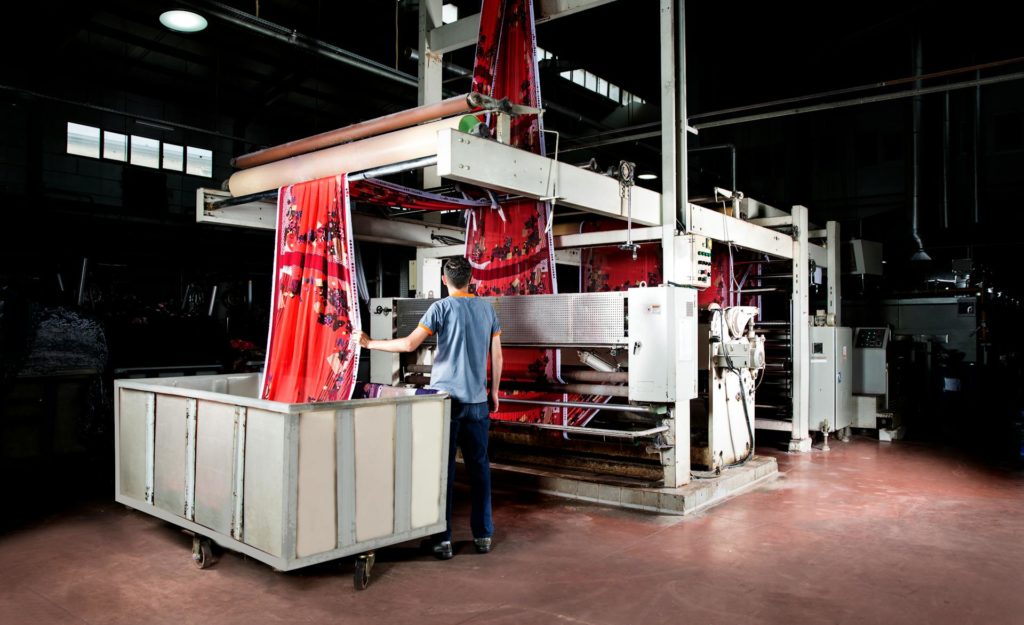
When it comes to manufacturing, cost-effectiveness, and quality are often seen as conflicting factors. However, in the case of injection molded products, the right strategies can lead to a perfect balance. In this blog post, we will explore key factors that contribute to achieving cost-effective quality injection molded products. By implementing these factors, businesses can streamline their manufacturing processes, reduce expenses, and deliver products that meet the highest standards.
Table of Contents
1. Material Selection
The costs and quality of injection molding depend a lot on materials. Choosing the right materials is essential for both cost-effectiveness and high quality in injection molding. High-quality resins may offer better mechanical properties but could also be more expensive. Manufacturers must strike a balance by selecting materials that achieve the desired product performance while keeping costs in check.
2. Mold Design Optimization
Mold design plays a crucial role in achieving cost-effective quality injection molded products. Optimizing the mold design can help minimize material waste and decrease production cycles by improving part release and reducing defects like warping or sink marks. Utilizing computer-aided design (CAD) software and virtual prototyping can effectively identify problematic areas before actual production.
3. Proper Venting
In injection molding, improper venting is one of the common causes of quality issues such as gas traps, short shots, or burns on the surface. Adequate venting ensures the timely escape of air or gases from molds during the filling process to reduce defects. Manufacturers can achieve optimal part quality by incorporating well-designed vents within mold cavities without jeopardizing production efficiency.
4. Process Optimization
Optimizing the injection molding process is crucial for maximizing productivity while maintaining product quality and ensuring cost-effectiveness. Variables such as melt temperature, flow rate, pressure settings, cooling time, fill rate, and holding time should be carefully monitored and adjusted as needed through experimentation or simulation studies that capture real-world scenarios.
5. Efficient Use of Resources
An essential aspect of achieving cost-effective quality injection molded products is making efficient use of resources. This entails managing energy, water, and raw material consumption to minimize waste and lower production costs. Utilizing advanced machinery with automatic functions can optimize resource usage while maintaining overall equipment effectiveness (OEE).
6. Quality Assurance Measures
Implementing stringent quality assurance measures throughout the manufacturing process is vital for delivering defect-free injection molded products at minimal cost. This includes regular inspection and testing, metrology controls, statistical process control (SPC), and documentation.
7. Supplier Partnerships
Establishing strategic partnerships with reputable suppliers is key to achieving cost-effective quality injection molded products. Collaborating closely with material suppliers and mold makers can yield benefits such as obtaining better pricing agreements, exclusive material options, or access to new technologies that enhance product quality while keeping production costs manageable.
8. Lifecycle Considerations
Effective management of the product lifecycle can significantly impact the overall cost-effectiveness of injection-molded products. Businesses should consider factors like design longevity, recyclability, upgradability, and ease of maintenance when developing their molding strategies. Opting for materials that are easily recyclable or exploring ways to extend the useful life of molds can lead to significant savings in the long run.
9. Automation and Robotics Integration
Integrating automation and robotics into injection molding can significantly increase cost-effectiveness and quality. Automated systems can handle repetitive tasks with precision, reducing the reliance on manual labor and minimizing the risk of human error. By implementing robotic arms, conveyors, automated part sorting, and other advanced technologies, manufacturers can achieve higher production rates, shorter cycle times, improved consistency in part quality, and reduced overall costs.
10. Continuous Improvement Initiatives
Continuous improvement is a cornerstone of achieving cost-effective quality injection molded products. Implementing lean manufacturing principles like Kaizen or Six Sigma methodologies allows businesses to identify and eliminate process inefficiencies. Through regular evaluation, analysis, and improvement implementation at every step of production – from design to delivery – manufacturers can optimize their operations while ensuring uncompromised product quality. A data-driven approach enables companies to identify opportunities for waste reduction, defect prevention, cycle time reduction, and unparalleled excellence in delivering high-quality products at competitive prices.
Conclusion
Achieving cost-effective, high-quality injection-molded products requires careful attention to several key factors. From material selection to mold design optimization, proper venting to process optimization, efficient resource utilization, and supplier partnerships, all play vital roles in maintaining a balance between cost-effectiveness and exceptional product quality. Additionally, integrating automation and robotics technologies into manufacturing and embracing continuous improvement initiatives further enhance efficiency.
By adopting these strategies and incorporating them into daily operations across different stages of product development—from design conceptualization to mold procurement to final batch production—manufacturers can deliver perfectly molded products that meet stringent quality regulations while remaining financially viable.