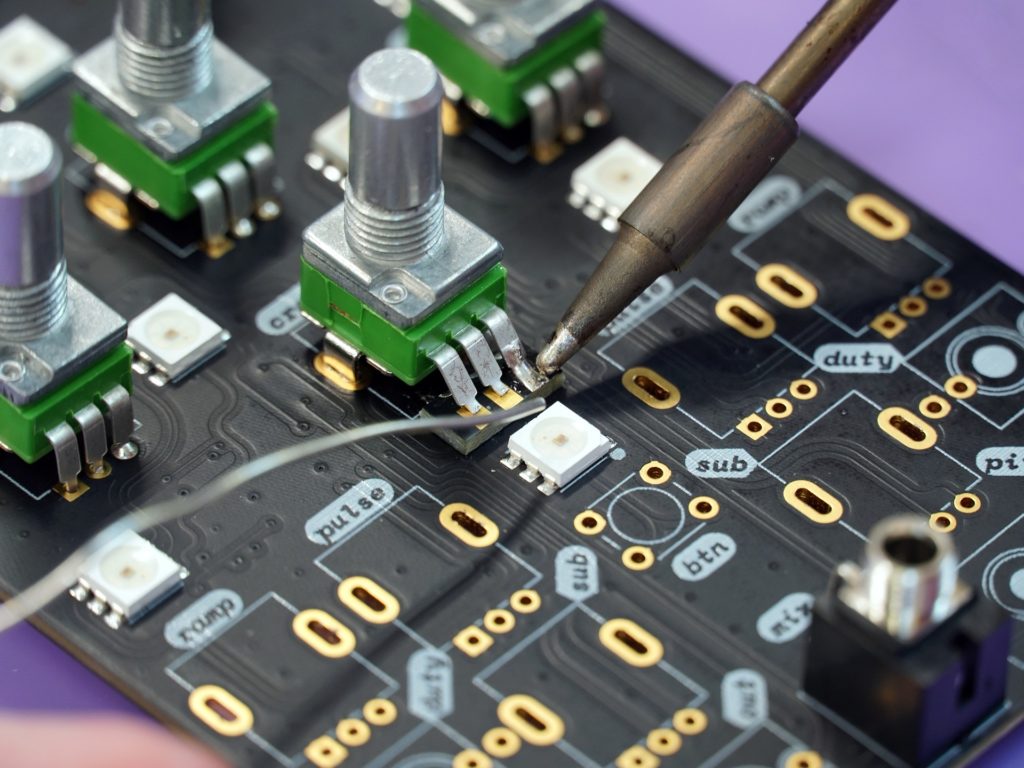
The consumer electronics industry is a significant sector, touching on a wide array of products from entertainment devices to musical instruments, marking a considerable impact on the global economy with expenditures reaching a trillion dollars in 2018.
Notably, smartphones lead sales, highlighting the scale and consumer demand in key markets such as China and the United States. Given this immense scale, the focus on adopting sustainable and efficient production methods is becoming increasingly crucial, not just for environmental responsibility but also for securing a sustainable future in a world heavily reliant on electronic devices.
Table of Contents
The Evolution of Electronics Manufacturing
The electronics manufacturing industry has witnessed a fluctuating trajectory over the last decade, as seen in the growth rates from 2012 to 2024. After an impressive 4.6% growth in 2012, there has been a noticeable variance in the subsequent years. A decline to a growth rate of 1% in 2015 reflects a possible stabilization or market saturation. However, a significant spike to 6% in 2018 suggests technological advancements or market expansions may have reinvigorated consumer interest and investment.
The dip into negative growth in 2020 likely mirrors the impact of the COVID-19 pandemic, with a quick rebound to a high of 9.6% in 2021 as industries adapted to new realities. Yet, the fluctuations continued with a contraction in 2023 at -3.96%. Regardless, projections for 2024 show a return to positive growth at 2.8%, suggesting resilience and adaptability in the sector.
Through this period, advances in technology, such as the integration of AI, IoT, and continued miniaturization, have driven the sector forward. These advancements have been crucial for the development of new products and have also introduced challenges and opportunities for sustainability and efficiency in manufacturing processes.
Sustainability is key
Sustainability in the electronics industry has transcended from being a mere trend to a fundamental operational necessity. This shift stems from the alarming levels of e-waste produced annually, underscored by the UN Global E-waste Monitor report in 2020, which reported a staggering 53.6 million tonnes of e-waste dumped worldwide in 2019.
In response, the industry is undertaking sustainable initiatives such as reducing hazardous materials in product design, improving energy efficiency, and adopting renewable energy in manufacturing processes. Notable examples include extended producer responsibility (EPR) programs, where manufacturers are encouraged to manage the lifecycle of electronic products responsibly.
Additionally, the adoption of a circular economy approach is gaining momentum. This model emphasizes the repair, refurbishment, and recycling of electronics, creating a closed-loop system that minimizes waste. Some companies are pioneering the use of biodegradable or recyclable materials for electronic products, while others invest in cutting-edge technology to increase the recyclability of electronic components.
Efficiency Challenges and Solutions
In the electronics manufacturing industry, achieving a balance between efficiency and quality is a perpetual challenge. Efficiency drives down costs and accelerates production times, while quality ensures reliability and longevity in electronic devices. Manufacturers employ innovative approaches to reconcile this dichotomy. Automation has been a key driver, allowing for precise and consistent assembly at high speeds. Real-time monitoring systems harness big data and IoT devices to streamline operations and predict maintenance, further optimizing production lines.
Another innovative method of enhancing efficiency is heat staking, which is used to join plastic and metal components. This technique offers a cleaner, faster, and more repeatable alternative to traditional methods like gluing or mechanical fastening. The non-invasive nature of heat staking means less stress on components, resulting in a higher-quality product. Additionally, because it requires no consumables, such as adhesives or screws, it is a more sustainable option that generates less waste.
Incorporating heat staking applications for industries is critical to advancing sustainability goals. This technique streamlines the assembly process, eliminating the need for additional materials, which complements the principles of the circular economy. Through heat staking applications, industries can enhance the durability and efficiency of their electronics manufacturing, effectively reducing the ecological footprint and meeting the growing consumer demands for environmentally responsible products.
Eco-friendly Practices
In the realm of sustainable and efficient manufacturing, companies like Patagonia, Toyota, and Interface stand as exemplars. Patagonia’s dedication to environmental stewardship is reflected in its renewable energy use and initiatives like “Worn Wear,” promoting a culture of reusing clothing. Toyota has made strides with lean manufacturing to reduce waste, championing resource conservation and end-of-life recycling. Interface’s “Mission Zero” highlights an ambitious pursuit to neutralize environmental impact, with significant reductions in greenhouse gas emissions and waste, and a commitment to carbon-neutral products.
The ripple effects of such practices are profound. When a leading outdoor clothing brand commits to sustainability, it influences not just its supply chain but also consumer behavior, inspiring a shift towards a more circular economy. Similarly, when a giant like Toyota streamlines its operations for eco-efficiency, it sets a new standard for the automotive industry, potentially leading to sector-wide advancements in sustainable practices.
Interface’s journey underscores the possibility of industrial transformation. By reducing its carbon footprint and prioritizing recycled materials, the company preserves the environment and showcases the economic viability of sustainable operations.
The impact of these companies’ actions extends beyond their immediate operational boundaries. They serve as benchmarks for environmental responsibility, spurring industry-wide innovations that aim to reconcile commercial success with the planet’s ecological health. Their successes prove that sustainable manufacturing is not only essential for environmental conservation but also advantageous for business resilience and consumer engagement.
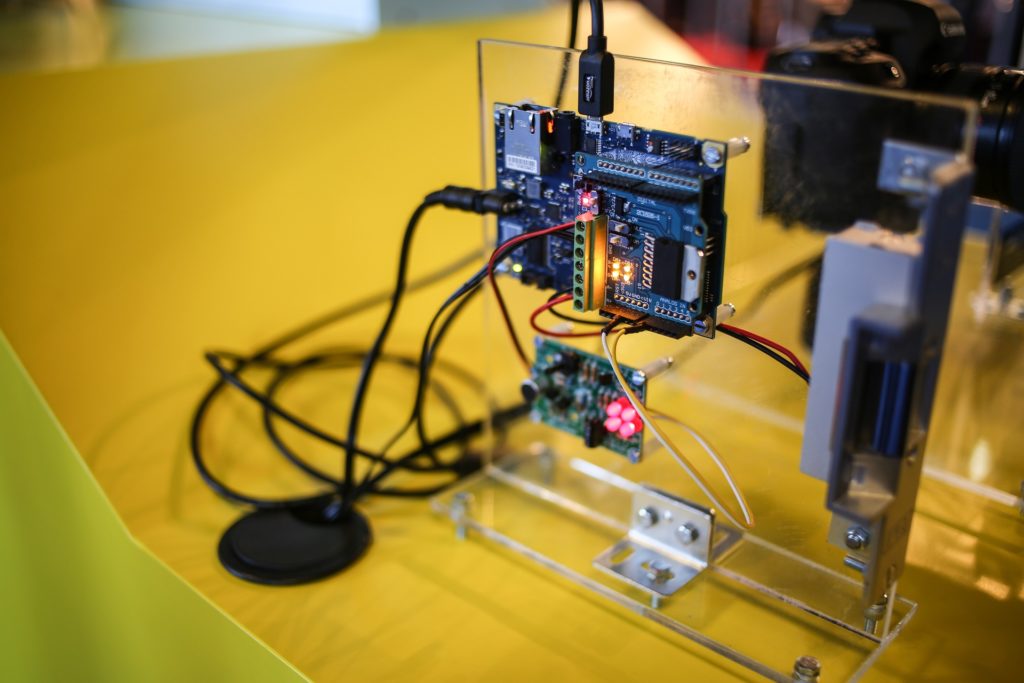
The Future Is Just Around the Corner
The future of electronics manufacturing is set to be dramatically reshaped by emerging technologies, significantly impacting sustainability and efficiency. Innovations such as 3D printing, advanced robotics, and nanotechnology are expected to streamline production processes, reduce waste, and lower energy consumption.
These technologies will facilitate the creation of more durable and energy-efficient electronic products, emphasizing the critical need for the industry to continue its pursuit of sustainable practices. As consumer awareness and regulatory demands for eco-friendly products increase, the industry’s ability to adapt and integrate these technologies will be paramount for future success, ensuring that electronics manufacturing evolves in harmony with environmental conservation goals.