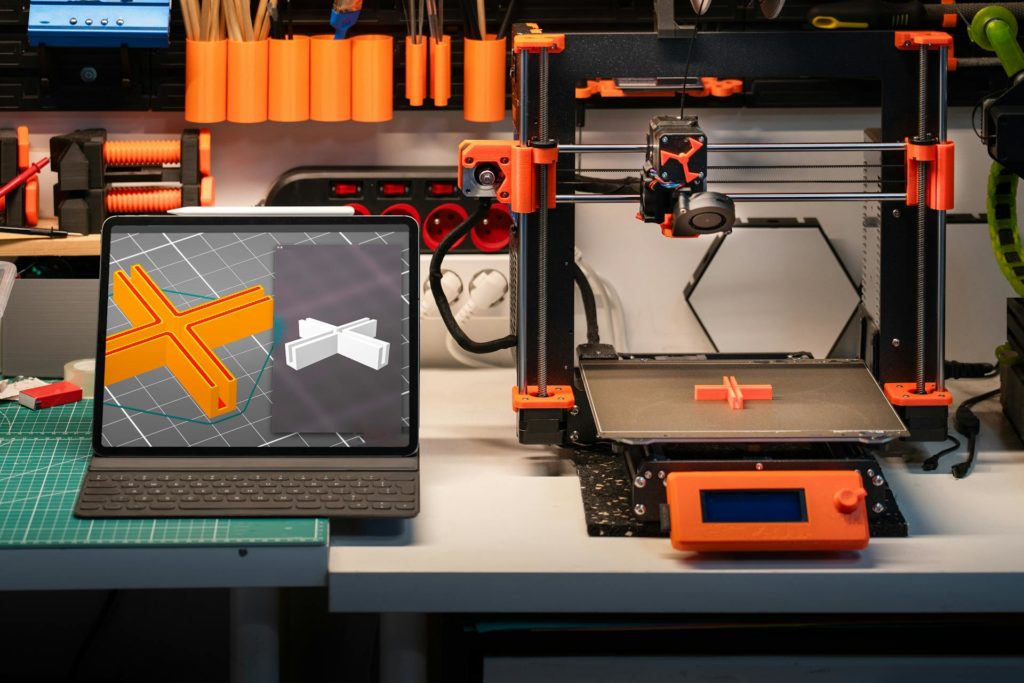
In recent years, 3D printing has transcended its origins as a niche technology and emerged as a disruptive force in manufacturing, design, and innovation. From rapid prototyping to end-use production, additive manufacturing has revolutionized countless industries, offering unprecedented flexibility, customization, and efficiency. At the forefront of this revolution are two distinct categories of 3D printers: hobbyist-level machines and industrial-grade systems. In this comprehensive guide, we will explore the evolution of 3D printing technology, examine the differences between hobbyist and industrial printers, and provide insights into when it might be advantageous to transition from a hobbyist setup to an industrial powerhouse.
Table of Contents
Understanding the Evolution of 3D Printing:
The origins of 3D printing can be traced back to the 1980s, with the invention of stereolithography (SLA) by Chuck Hull. This groundbreaking technology paved the way for additive manufacturing, enabling the layer-by-layer fabrication of three-dimensional objects from digital designs. Initially used primarily for prototyping purposes, 3D printing gradually expanded its reach, with the development of new materials, processes, and applications.
The early years of 3D printing were characterized by high costs, limited material options, and relatively slow print speeds. However, as the technology matured and became more accessible, a new market emerged: the hobbyist 3D printing community. Hobbyist-level printers, often based on fused filament fabrication (FFF) or SLA technology, offered enthusiasts, educators, and makers the opportunity to explore the world of additive manufacturing from the comfort of their own homes or workshops.
The Rise of Hobbyist 3D Printing:
Hobby 3D Printer: Image Source: trimech.com
The democratization of 3D printing can largely be attributed to the rise of hobbyist-level machines. These compact, affordable printers opened up new possibilities for creative expression, experimentation, and learning. Hobbyists could now bring their ideas to life in tangible form, whether custom prototypes, personalized gifts, or intricate works of art.
Hobbyist printers typically utilize FFF technology, which involves extruding thermoplastic filament through a heated nozzle to build up layers of material. This process is relatively simple and straightforward, making it ideal for beginners and enthusiasts. Similarly, SLA printers use a liquid resin cured layer by layer using a UV light source, offering higher resolution and finer details than FFF printers.
Challenges with Hobbyist Printers:
While hobbyist-level printers have undoubtedly lowered the barrier to entry for 3D printing, they come with their own challenges. One of the primary drawbacks is print quality and reliability. Hobbyist printers often need help to maintain consistent print quality, resulting in issues such as layer misalignment, warping, and surface imperfections. Users may spend hours troubleshooting and fine-tuning their machines to achieve satisfactory results, detracting from the overall user experience.
Another limitation of hobbyist printers is material compatibility. While they offer a wide range of thermoplastic filaments and resins, hobbyist printers may not support specialized or high-performance materials required for certain applications. Additionally, hobbyist printers typically have smaller build volumes, limiting the size of objects that can be produced in a single print. This can be particularly frustrating for users working on larger projects or batch production runs.
The Promise of Industrial 3D Printing:
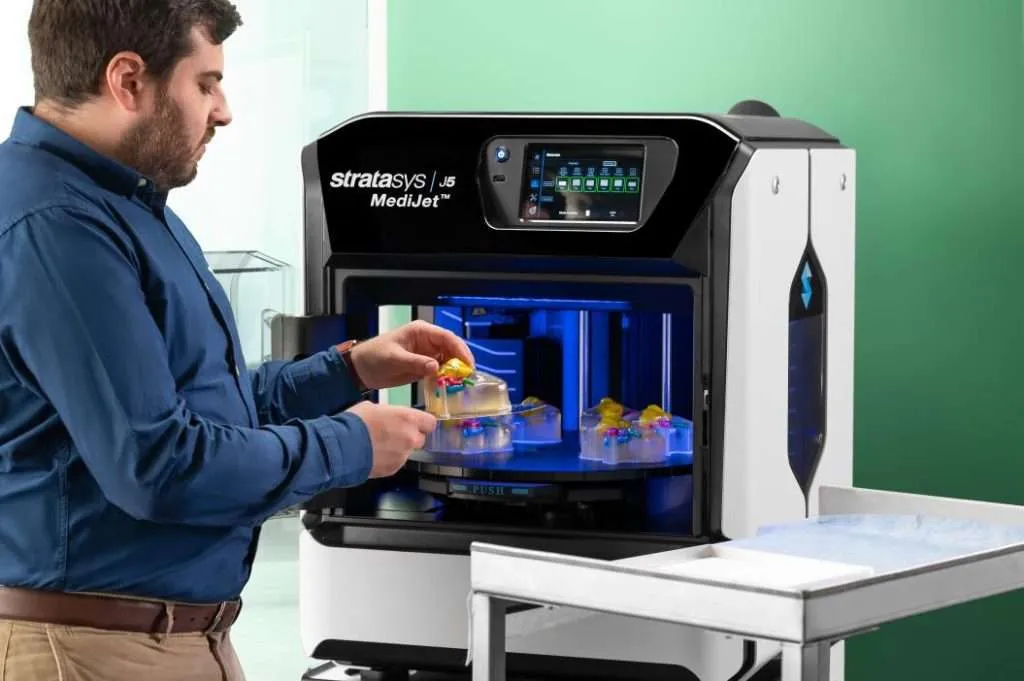
Industrial 3D Printer: Image Source: trimech.com
In contrast to hobbyist printers, industrial-grade 3D printers offer a level of performance and versatility that is unmatched in the consumer market. These machines are designed for reliability, precision, and scalability, making them ideal for many professional applications. Industrial printers utilize advanced technologies such as Selective Laser Sintering (SLS), Multi-fusion (MJF), or PolyJet, producing highly detailed, complex parts with exceptional accuracy and surface finish.
Key Considerations for Upgrading:
Making the transition from a hobbyist printer to an industrial-grade system is a significant decision that requires careful consideration. Several factors should be taken into account when evaluating whether an upgrade is warranted:
1. Reliability: Industrial printers are engineered for continuous operation and are equipped with features such as automated calibration, active temperature control, and advanced print monitoring systems to minimize the risk of print failures.
2. Precision: Industrial printers offer superior dimensional accuracy and surface finish, allowing for the production of parts with tight tolerances and intricate geometries.
3. Material Compatibility: Industrial printers support a wide range of engineering-grade materials, including high-performance thermoplastics, metal alloys, and composite materials, expanding the possibilities for functional prototyping and end-use production.
4. Build Volume: Industrial printers typically have larger build volumes than hobbyist machines, enabling the production of larger parts or batch printing of multiple components simultaneously.
5. Workflow Integration: Industrial printers are often compatible with software platforms and workflow management tools that streamline the design, preparation, and printing process, reducing manual intervention and maximizing productivity.
Case Studies and Success Stories:
To illustrate the benefits of upgrading to an industrial-grade 3D printer, let’s explore several real-world examples of businesses and organizations that have made the transition successfully.
- Automotive Manufacturing: An automotive manufacturer adopts industrial-grade 3D printing technology to produce custom tooling, fixtures, and end-use parts for its production line, reducing lead times and improving overall efficiency.
- Healthcare Innovation: A medical device company leverages industrial 3D printing to develop patient-specific implants and surgical guides, revolutionizing the field of personalized medicine and improving patient outcomes.
- Aerospace Engineering: An aerospace engineering firm utilizes advanced additive manufacturing techniques to produce lightweight, complex components for aircraft and spacecraft, reducing weight, fuel consumption, and production costs.
Best Practices for Implementation:
Transitioning to an industrial-grade 3D printing solution requires careful planning and execution to ensure a smooth integration into existing workflows and processes. Key considerations include:
1. Conducting a thorough needs assessment to identify specific requirements and objectives.
2. Evaluating different printer models and technologies to find the best fit for your application.
3. Invest in training and support services to ensure that users are proficient in operating the new equipment.
4. Establishing quality control procedures and performance metrics to monitor and optimize print output.
5. Leveraging networking opportunities and industry partnerships to stay informed about the latest developments and best practices in additive manufacturing.
SelfCAD: Easy 3D Modeling for Beginners and Pros
SelfCAD: Easy 3D Modeling for Beginners and Pros: Image Source: selfcad.com
SelfCAD is a 3D modeling software that helps people create 3D models. You can use it in your web browser or download it to your computer. It doesn’t matter if you’re just starting out or if you’re already a pro at making 3D models – SelfCAD is for everyone. It’s designed to be easy to use, so even beginners can make cool 3D stuff without a lot of hassle.
There are lots of resources available to help you learn how to use SelfCAD. You can watch videos, follow interactive tutorials, or read detailed guides. And if you ever get stuck, there’s plenty of help available.
One of the best features of SelfCAD is its slicing software. This lets you get your designs ready for 3D printing, so you can turn your virtual creations into real-life objects. But that’s not all – SelfCAD also has tools for sculpting, sketching, and rendering. You can even start with pre-made shapes and customize them to make something totally unique.
If you’re more into 2D drawing, SelfCAD has you covered there too. You can draw sketches and turn them into 3D models with just a few clicks. And once you’ve made something awesome, you can easily share it with others and work together on projects.
SelfCAD offers different pricing plans to fit your needs. There’s a free plan that lets you make and export three drawings every month. If you need more than that, you can sign up for a paid subscription starting at $14.99 per month. With a paid subscription, you get unlimited access to all of SelfCAD’s features, including exporting, 3D printing, and rendering.
So whether you’re a total beginner or a seasoned pro, SelfCAD has everything you need to bring your 3D creations to life. Give it some effort and see what you can create!
Conclusion:
As a whole, the development of 3D printing marked a new era filled with creativity and opportunity. While hobbyist-level printers have played a crucial role in democratizing access to additive manufacturing technology, they may not be suitable for demanding professional applications. Industrial-grade printers offer unparalleled performance, reliability, and versatility, empowering businesses to unlock new opportunities and drive innovation. By carefully evaluating the specific needs and goals of your organization and leveraging the expertise of industry professionals, you can make a well-informed decision that positions you for success in the rapidly evolving world of additive manufacturing.