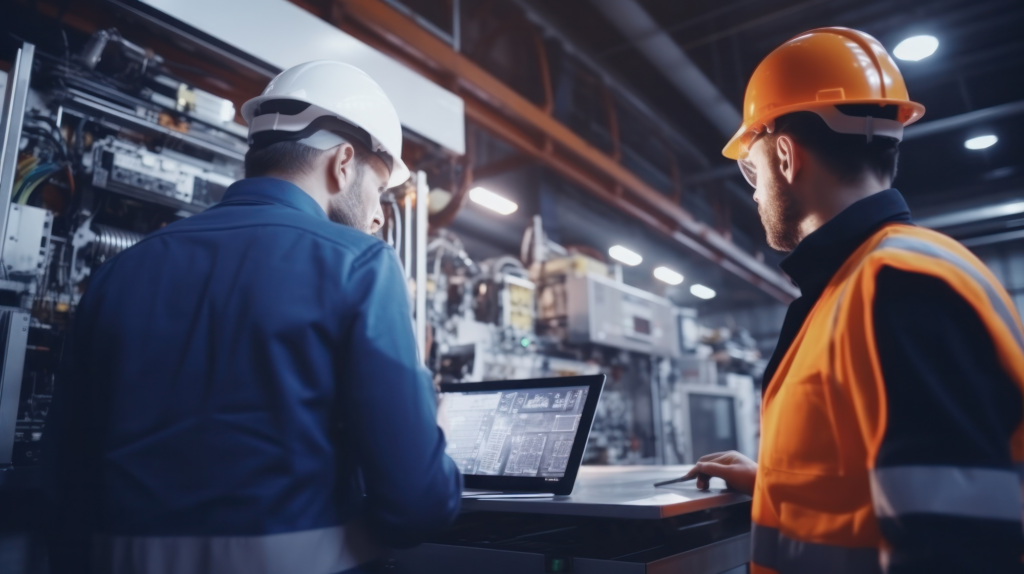
Modern processing equipment is designed with efficiency in mind at every level. From manufacturing lines to data centers, the features that maximize efficiency enable greater throughput, reduce waste, and optimize resources.
Read on to explore some of the critical features that help achieve optimal efficiency across various industries and applications:
Table of Contents
1.Automation And Control Systems
Automation transforms production through controlled technologies that minimize human error and maximize efficiency. For instance, automated inspection systems utilize high-resolution cameras and sensors for accurate defect detection. Conversely, advanced robotic systems seamlessly transfer components between workstations with unparalleled speed and precision.
Beyond manufacturing, complex machine learning algorithms analyze massive datasets to uncover patterns and generate insights at a scale no human can achieve. For example, automated credit approval systems can synthesize thousands of data points to provide customized loan terms. Likewise, automated ordering kiosks allow customers to customize meals and skip restaurant lines.
Automation enhances complex operations in diverse sectors by pairing human cognitive abilities with rapid and precise automated execution. The best part is that you can access these equipment easily if you don’t have them already. Consider visiting Milestone-equipment.com to find various automation solutions and machine vision inspection equipment from leading manufacturers.
2.High-Performance Components And Design
Cutting-edge processing equipment incorporates advanced components engineered for maximum durability and optimal efficiency. Use precision-balanced motors with patented magnetic bearing systems to eliminate maintenance while providing seamless variable speed control. Consider smart sensors to enable predictive maintenance by monitoring vibration to minimize downtime.
Also, ergonomically designed features focused on user comfort, such as height-adjustable workstations and intuitive control interfaces, help minimize physical strain and fatigue for operators. For instance, an ergonomic forklift incorporates swivel seats, lumbar supports, and angled floorboards to reduce fatigue over long shifts.
Additionally, durable, lightweight composites replace traditional materials in demanding environments prone to corrosion. Thermoset plastics withstand caustic chemicals without degrading, while nanoceramic coatings drastically increase equipment lifespan.
Component innovations and human-focused design enable you to maintain a sustainable and reliable throughput vital to modern operations. Also, next-generation processing equipment achieves maximum safety, productivity, and longevity by melding high-tech materials, streamlined maintenance, and your team’s well-being.
3.Integration And Interconnectivity
Processing equipment seamlessly networks with robots, control systems, and enterprise layers through system-wide integration. This creates a highly interconnected production environment.
Interconnectivity fosters flexibility and responsiveness, allowing machines to share real-time data. This enables centralized monitoring, rapid bottleneck diagnosis, and collaborative robot task optimization for improved workflow.
Integration propels the next generation of adaptive, automated processes for transformative efficiency. Quality control systems instantly compare readings across stations to pinpoint deviations. Modern processors gain a system-wide perspective by linking automation into a cohesive ecosystem. This empowers continual optimization through machine learning.
4.Modularity And Scalability
Today’s processing equipment champions versatility through customizable configurations that meet diverse production goals. Modular systems provide the flexibility to customize components for your unique production requirements, eliminating the limitations of generic, standardized equipment. For example, food processors can outfit machines with hygienic parts well-suited for sanitary environments.
Manufacturers also provide attachments like conveyors, hoppers, and robotic arms to build optimized workflows. Rapid changeover systems and retrofit kits allow you to enhance current machinery, future-proofing your operations as needs evolve. Rather than a static purchase, modern processors offer an adaptable foundation for developing business demands. You can effortlessly scale up bottling speed by adding modular stations when you expand your business operations.
Additionally, customization empowers factories to respond quickly to market shifts or new opportunities. By selecting from specialized components, processors gain bespoke solutions while avoiding overinvestment. Customization delivers versatile, agile equipment engineered for long-term success across industries.
5.Data Acquisition And Analytics
Modern equipment harnesses real-time data to optimize performance through analytics-driven intelligence. You can integrate precision sensors to capture detailed real-time data on operational parameters such as vibration levels, temperatures, and energy consumption, creating a digital twin of the process for in-depth analysis.
Cloud-based analytics platforms apply machine learning algorithms to identify inefficiencies and predict failures before they occur. For example, if pipeline pressure readings show even minor deviations from normal parameters, the system automatically schedules proactive maintenance to prevent potential leaks before they occur.
Data analytics empowers continuous enhancement by connecting your equipment engineers with uptime, yield, and sustainability parameters. Insights trigger proactive adjustments instead of reactive fixes. By enabling data-driven decision-making, smart processing equipment leverages advanced analytics to drive maximum utilization, quality, and reliability while minimizing waste.
6.User-Friendly Interfaces And Operator Training
This equipment also prioritizes usability through intuitive interfaces and immersive training tailored to your operation needs. For one, innovative touchscreen interfaces featuring visual dashboards replace text-heavy manuals, using graphical step-by-step guidance to streamline equipment control and troubleshooting.
On-demand contextual help includes step-by-step maintenance animations. Virtual and augmented reality simulations build competency by immersing trainees in lifelike procedural practice without risk. Following classroom education, hands-on apprenticeships with experienced mentors cement skills. Also, training continues through the equipment lifespan with refreshers and new module certifications.
Contemporary, intuitive interfaces and comprehensive training empower your operations team by simplifying sophisticated equipment and cultivating expertise, self-assurance, and workplace safety. User-centric design fosters human-technology collaboration versus deep expertise. Anyone can effectively harness sophisticated systems with a suitable human-machine interface and support.
7.Remote Monitoring And Diagnostics
Cutting-edge equipment applies cloud-based technologies for real-time remote oversight, minimizing downtime. Secure data transfers provide access to system health anywhere, anytime. This enables proactive instead of reactive service through instant issue identification and rapid solutions.
You can use diagnostic dashboards to track hundreds of sensor inputs from multiple equipment units in diverse locations simultaneously. At the first indication of any issues, your team can remotely diagnose the cause, identify required replacement parts, and quickly coordinate service technician dispatch.
You also benefit from on-screen support guiding on-site maintenance. For example, if a packaging machine triggers an alarm, an engineer can remotely control the operator by replacing a worn belt based on real-time data.
Preventive interventions driven by performance trends optimize uptime. Remote capabilities transform customer service from days-long repairs into minute-long solutions. By combining round-the-clock insights with rapid response, advanced processing systems sustain maximum production quality and efficiency through pioneering connectivity.
8.Cybersecurity And Data Protection
Networked equipment demands rigorous cybersecurity to safeguard sensitive operational data and intellectual property. Multi-layered cybersecurity, including firewalls and encryption protocols, secures sensitive data by identifying and blocking any unauthorized attempts to access systems. Authentication protocols authorize information exchange only between validated systems, quarantining risks. Also, cloud-based data storage leverages enterprise-grade security, including frequent patching and redundant backups.
Implement strict internal controls to govern data access and modification following industry best practices. For example, a team member not authorized to change the system configurations can only view but not alter sensor data, which requires security clearance.
Periodic third-party security audits and continuous team training are essential to identify potential vulnerabilities and maintain diligent cybersecurity practices. Implementing overlapping digital and organizational measures aligned to standards allows you to secure your proprietary knowledge and maintain a competitive edge.
9.Additive Manufacturing
Additive manufacturing, or 3D printing, has revolutionized processing equipment design, prototype, and manufacturing. This technology offers unparalleled flexibility and speed, enabling rapid innovation in the industry.
One primary application of 3D printing is rapid prototyping. Your engineers can quickly create physical models of proposed designs, allowing them to test and refine their ideas before committing to costly production runs. For instance, a manufacturer might 3D print a prototype of a new robotic gripper to evaluate its form, fit, and function in real-world conditions.
3D printing also plays a role in creating custom tooling and fixtures for processing equipment. Instead of relying on traditional manufacturing methods, which can be time-consuming and expensive for low-volume production, 3D printing creates unique tools tailored to specific applications. For example, a food processing plant can use 3D-printed cutting dies to create intricate shapes in a new line of baked goods.
Additionally, you can use additive manufacturing to produce end-use components for processing equipment. For instance, some manufacturers use 3D-printed metal parts in their machinery, taking advantage of the technology’s capabilities to develop complex geometries that may be challenging to achieve through traditional means. Conversely, a chemical company might use 3D-printed impellers in their centrifugal pumps, optimizing their design for improved efficiency and performance.
10.Sustainability And Resource Conservation
Sustainable equipment minimizes environmental impact through efficiency. Intelligent process controls regulate energy and material flows to avoid waste. Smart metering collects granular data for optimization; compressed air leaks get quickly identified and resolved. Also, sensors maintain ideal temperature and humidity levels for each stage instead of over-conditioning the entire facility.
Recirculating water systems reuse precious resources, and you can recover and repurpose heat for facility heating or prewarming inputs. Some installations return surplus energy to the grid. For example, an anaerobic digester at a dairy farm converts waste into renewable biogas energy. Proactive maintenance further extends lifespan by anticipating needs.
Generally, achieving sustainability demands a comprehensive evaluation of the entire system. Although efficiency upgrades like LED lighting provide meaningful progress, redesigning processes centered around reuse and regenerative principles enables breakthrough environmental performance. By matching rigorous analytics with circular thinking, modern equipment elevates environmental stewardship from cost to opportunity through holistic innovation beyond quick fixes.
11.Continuous Innovation And Upgrades
The future of processing technology lies in continuous innovation, not sporadic breakthroughs. Committed manufacturers relentlessly stretch possibilities through customer-centric development.
For example, a packaging equipment company might partner with a supplement provider to engineer flexible solutions accommodating various bottle and pouch designs. Regular software upgrades then optimize those machines based on user feedback and emerging needs.
Also, modular hardware upgrades like improved sensors or extrusion heads help legacy machinery deliver next-generation performance. Some suppliers offer full factory simulations to model upgrade benefits before installation. This failsafe experimentation accelerates improvement.
While new technologies make headlines, incremental advances collectively drive transformative progress. Equipment builders ensure upgrades align with evolving real-world demands by maintaining strong customer relationships through sustained collaborative innovation.
Conclusion
Maximizing efficiency in modern processing equipment requires a multifaceted approach leveraging cutting-edge technologies. Critical features include automation, intelligent analytics, optimized design, user-centric interfaces, and continuous innovation to drive speed, quality, and cost-effectiveness.
Aligning equipment with operational needs through flexibility and proactive solutions gives you a competitive edge. Remember, efficiency is the guiding principle for processing technology. With these critical capabilities, you can achieve remarkable speed, quality, productivity, and cost-effectiveness.