In theory, the manufacturing of small/mid-size industrial parts requires the same cutting action and chip formation methods.
However, one of the biggest challenges facing this sector is the need for cost reduction. Automakers, for instance, are constantly reducing their pricing, which, in turn, forces businesses to look for more cost-effective production processes. Of course, while doing this, manufacturers still need to increase their efficiency and productivity to remain competitive in the market.
The manufacturers of large industrial parts are no exception when it comes to production challenges. These parts demand a well thought of approach to machining and a predefined process. The manufacturing of prefab stairs, for instance, requires a lot of planning in terms of costs, raw materials, and the safety of the final user. But, what can be considered the biggest challenge in this industry? Read on to learn more!
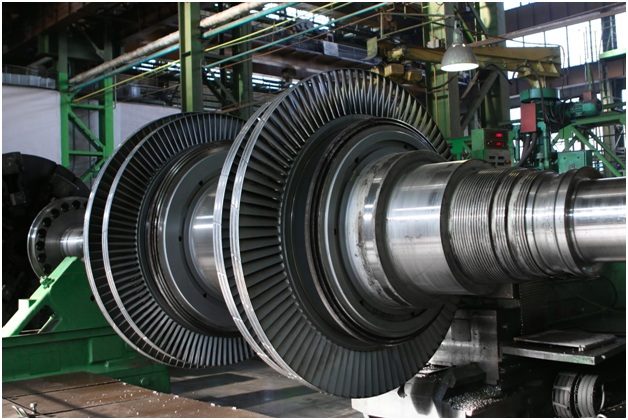
Table of Contents
The Challenge
The biggest challenge with manufacturing large industrial parts is the amount of space it takes up. For a more efficient process, the facility needs to be spacious enough not only for the assembly of these large parts, but also to allow the free movement of the employees. Mounting the part in the machine tool, clamping, and initial setup is far more challenging than for the small to medium-sized products and often demands a non-standard approach that comes with years of experience in manufacturing large parts for massive companies.
Another reason, large part manufacturing is problematic is due to its specific dimensions and risk of thermal expansion during cutting. Appropriate chip evacuation for preventing chip recutting is required to remove a significant machine stock.
How to Overcome the Challenge
The key to overcoming these challenges lies in the simplicity of the setup, which requires exceptional pre-planning along with adequate machine tools. Having highly precise tools that can ensure optimal withholding of the material is paramount for an ideal large part manufacturing setup. Moreover, to ensure the dimensions are achieved, it is highly essential to maintain minimal part relocation.
The tool life and reliability are the two most important factors in a successful large part manufacturing company as the large parts demand higher running time of the tools than normal. The breakage of the tool while large part manufacturing is not only catastrophic but also requires high replacement costs.
There are many industries such as aerospace, railway, power generation, and other high reliability demanding heavy industries that appeal for highly precise and accurate manufacturing of large heavy-duty parts. These industries require a smart combination of industry-standard and special designs that can be provided by industry veterans like https://www.ceratizit.com/.
Final Thoughts
Industries relying upon heavy-duty large parts demand high reliability, stability, and precision. Although the process of manufacturing these large parts might seem identical to medium-size production, the expertise and resources of a well-experienced producer are unparalleled.
With all these in mind, you can see why every company in this industry requires personnel with a lot of expertise. Of course, all the necessary training can be done. However, without enough experience, the productivity will either slow down, or the market will be fed with substandard products.
The failure in the machinery that uses large parts usually has the capacity to create a largely negative impact. You know that any accident caused by failed machinery can be fatal for the unsuspecting end user. Therefore, it is important to produce them with as much precision and reliability as possible.