Efficiency is one of the central factors in building a profitable, sustainable, and environmentally friendly production line, and finding ways to cut out bottlenecks and reduce energy consumption has been a key goal of contemporary industrial strategy and planning.
But sometimes the only way to reduce your overall energy use while increasing the speed and effectiveness with which you can produce goods is by investing in new technology that incorporates scientific innovation to reduce energy waste.
This article explores how improvements to equipment in one area of industrial production — heat exchange — can have a major impact on the overall energy profile of a factory or production line.
Heat Exchange: An Essential Aspect of Modern Manufacturing
Whether you are processing coffee, olives, sugar, or plastics, if you are in the business of producing bulk solids, cooling, heating, and drying are going to be essential aspects of your operation.
Because these processes (generally referred to as “heat exchange”) involve dramatic and stable changes in temperature for large quantities of material, they tend to be fairly energy-intensive. And because they result in energy as a by-product, they can be quite wasteful.
Think about a drum-style air dryer that processes coffee beans: most of the heat generated to heat the beans will simply be diffused and dispersed. Not only does this increase overall energy costs, it also means that most of the energy generated will be wasted.
Unfortunately, for most industrial processes heat exchange is absolutely essential, which is why manufacturers have had to live with this expense for decades. But with new technology making it easier to transition away from wasteful heat exchange processes, things are starting to change.
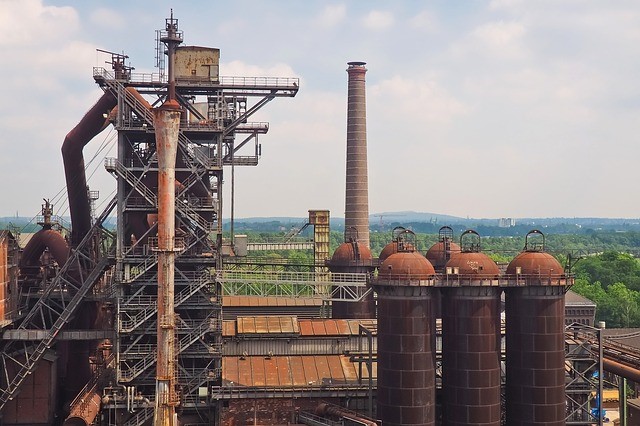
How Modern Heat Exchangers are Making a Difference
Given the energy-intensive nature of heat exchange processes, it shouldn’t be surprising that attempts to improve the overall efficiency of production lines focus on making heat exchange more efficient.
To this end, many manufacturers are investing in new equipment that can make heat exchange smarter and more sustainable. One of the most efficient of these new exchangers is the cooling tower heat exchanger, which can reduce the energy use involved in heat exchange by as much as ninety percent.
But what is a cooling tower heat exchanger — and how does it work? A cooling tower heat exchanger uses ceramic panels to process bulk solids with the help of gravity. The panels allow for a more targeted and controlled exchange of heat which allows almost all of the energy to be recycled back into the system, reducing energy costs while also providing a more effective way of cooling, heating, and drying bulk solids.
Using these new heat exchangers, production lines can achieve major financial savings, while reducing the amount of maintenance needed to keep their exchangers in good working condition.
Efficiency is important not only because it helps you get more done with the same or fewer inputs. Given the global challenge of switching from fossil fuels to renewables like wind, solar, biomass, and nuclear energy, finding more efficient ways to produce everything from comestibles to plastics is essential to mitigate the worst effects of climate change.
By reducing the amount of energy used and improving energy retention and storage, modern heat exchangers are playing an essential role in building a more sustainable future for manufacturing.